1 超音速火焰喷涂
20世纪80年代,超音速火焰喷涂(HVOF)工艺研发成功。HVOF将粉末、丝材或棒材送入超音速的高温焰流中,加热熔融后并喷射到基材形成涂层。一般情况下,焰流速度可达到5马赫(1500m/s)以上,熔融颗粒在火焰中可被加速到300~700m/s,甚至更高。
超音速火焰喷涂粒子的温度低、飞行速度快,因此涂层的结合强度高、孔隙率更低。HVOF工艺可以喷涂各种硬质合金材料,包括纳米结构粉末。Manzat等采用超音速火焰喷涂(HVOF)和超音速悬浮液火焰喷涂(HVSFS)方式,分别在气缸内壁制备出金属和陶瓷涂层,涂层表面具有大量直径为0.2~1.0μm的贯通孔隙,这些孔隙能够储油,形成微负压室并实现液态润滑。Johansson等也用HVOF和HVSFS方式制备出铁合金、Cr3C2/NiCr、80%TiO2-20%TiC和铁基复合材料(MMC)涂层,研究结果和Manzat等基本一致,该涂层的磨损量显著低于铸铁缸套的磨损量,其中Cr3C2/NiCr和MMC涂层的磨损量低于80%TiO2-20%TiC。
超音速火焰喷涂制备的涂层还具有结合强度高的特点,毛俊元等通过HVOF方法在球墨铸铁气缸套内壁上制备NiCrBSi合金涂层,涂层的结合强度达到128.8MPa。此外,NiCrBSi涂层在常温和高温下均具有良好的耐磨耐腐蚀性,由于燃料中含有硫元素,会在气缸壁生成硫酸,在表面形成硫酸腐蚀。实验采用30%(质量分数)稀硫酸和8%(质量分数)稀盐酸作为腐蚀剂,将喷涂好的涂层浸泡在腐蚀剂中一个月,通过光谱分析涂层浸泡前后的化学成分,发现涂层化学成分变化十分小。如将该涂层应用在气缸套上,能增大气缸套的耐腐蚀性能,延长气缸套的使用寿命。
Edrisy等针对低碳钢气缸内壁涂层,分别探讨了涂层在销盘摩擦中和在实际使用中的耐磨性以及拉缸损坏情况。结果表明,铝合金气缸内壁的低碳钢涂层在实验室磨损测试条件下展现出很好的耐磨性。在实际应用中,气缸壁磨损最严重的地方发生在最大推力面处,在燃烧动力冲程循环过程中,由于施加较大的负载,导致在涂层下面产生单一方向的塑性变形层,剥离是磨损的主要形式。
2 电弧喷涂
电弧喷涂是利用两根连续送进的金属丝之间的电弧来熔化金属,用高速气流把熔化的金属雾化,并迅速喷射到基材表面形成涂层。电弧喷涂因易操作、效率高、对工件热影响小、涂层性能优异、适用范围广及经济安全等特点而得到迅速发展,到20世纪末,电弧喷涂的应用占所有热喷涂的15%,市场比例位居第3位。目前,国外使用电弧喷涂制备气缸内壁涂层的报道并不多,而国内学者做了较多的工作。
李增荣、吴比等设计并制造的XDP-5型内孔电弧喷涂设备,解决了发动机气缸内壁难以喷涂的问题。他们选用铁基合金金属丝材制备铝制缸体内壁减摩涂层以代替铸铁缸套,涂层由扁平粒子堆积而成,在颗粒边界还存在一些孔隙和带状金属氧化物。摩擦磨损结果表明,涂层孔隙结构的储油效应和表面氧化物起到明显降低摩擦系数的作用,提高了涂层的耐磨性。
Kim等采用双丝电弧喷涂(TWAS)在铝合金气缸套内壁制备FeO涂层,研究珩磨工艺对内壁涂层的影响。两种珩磨的气缸内壁涂层分别是40°珩磨角的光滑层(SH)和140°珩磨角的螺纹结构珩磨层(HSH),如图1所示。在干摩条件下,由于HSH的珩磨槽更大,可以留住磨粒因而避免磨粒磨损,所以HSH层的摩擦系数更低。在润滑条件下,由于SH层的表面更加光滑,因此具有较低的摩擦系数。综合来讲,采用TWAS工艺制备的气缸内壁涂层即使在恶劣的发动机工作条件下,仍可以展现优异的摩擦性能。
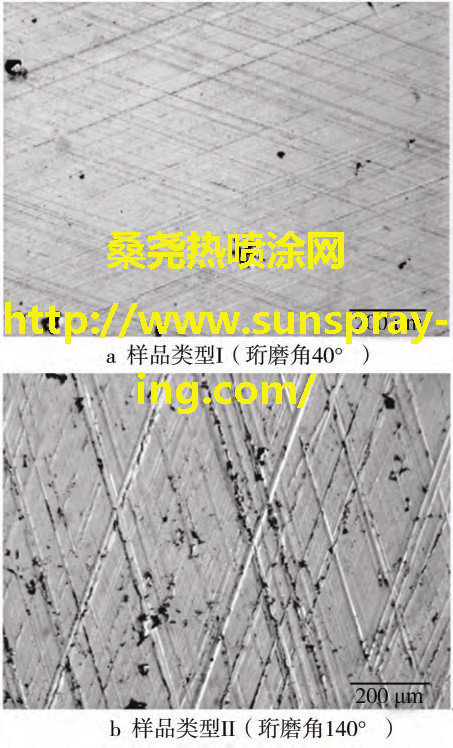
图1 气缸内壁样品表面交叉珩磨纹路
Fig.1 Surface topography of cylinder liner specimens showing cross hatch honing pattern: a) type I specimen (honing an- gle~40°) and b) type II specimen (honing angle~140°)
采用电弧喷涂技术也可对气缸套进行修复。吉荣廷等采用电弧喷涂对内燃机缸套内表面进行修复,恢复缸套的尺寸,修复成本仅为新缸套的1/3,而修复好的缸套的使用寿命可以达到原缸套的3倍。因此,无论从经济效益还是社会效益来看,电弧喷涂工艺修复内燃机缸套都是一种理想的方法。曾志龙、徐亮等针对大型船舶柴油机气缸套腐蚀磨损失效情况,采用高速电弧喷涂和亚音速火焰喷涂工艺,对失效气缸套进行再制造并进行摩擦磨损实验。研究表明,在实际运行工况下,电弧喷涂的3Cr13涂层表现出的性能优于火焰喷涂的NiCr-Cr3C2涂层,且电弧喷涂成本较低,该技术有望在气缸套再制造中得到应用。
3 大气等离子喷涂
大气等离子喷涂(APS)通过放电生成的热等离子(15000K)将粉末材料熔化并喷射到基体表面形成涂层。这种工艺适合喷涂各种熔点高的粉末材料,尤其是复合材料和陶瓷材料。20世纪90年代初,SulzerMetco公司(OerlikonMetco前身)开发了“RotaPlasma”旋转式APS喷涂设备,至今仍被很多制造商用于喷涂发动机气缸内壁涂层。在过去几年中,APS技术不断改进发展,有关APS内孔涂层工艺和材料选择的进展已有很多外文文献报道。
在原始粉末中加入其他元素可以有效提高APS涂层的综合使用性能。Uozato等研究了APS喷涂铁基合金粉(Fe-C-Ni-Cr-Cu-V-B)中添加不同含量Ni粉所得柴油机气缸内壁涂层的耐磨耐腐蚀性并与常用铸铁缸套进行比较。摩擦实验结果表明,铁基涂层的磨痕深度最大值小于铸铁缸套磨痕深度的一半,并且摩擦对偶销的磨损深度也低于铸铁缸套对偶销。在实际应用中,不仅要保证气缸内壁耐磨,同时要减少对活塞环的磨损,采用这种涂层可增加活塞环的使用寿命。在原始铁基粉中加入质量分数4%~14%的Ni粉以后,涂层在硫酸溶液中的耐腐蚀性随Ni含量增加而提高,且远远优于铸铁材料,但与此同时,在油润滑下涂层的耐磨性随Ni含量的增加而降低,这主要由于Ni的添加降低了涂层硬度。因此,合适的Ni含量,将有助于平衡涂层的耐磨性和耐蚀性。
APS焰流速度高,粉末颗粒速度快,喷涂时采用Ar等惰性气体,因此所得涂层的致密度和结合强度都很高,且涂层的氧化物和杂质含量少。Kim等采用APS工艺在铝合金基体上分别喷涂了水雾化得到的铸铁(Fe-3.75C-3.6Si-3.93Al)粉末和经过退火预处理含有石墨结构的铸铁粉,获得涂层C1和C2。浸泡腐蚀结果表明,涂层的耐蚀性主要取决于孔隙率,两种涂层的孔隙率均较低,分别为4.33%和3.4%。C1涂层表面和截面形貌都有明显改变,存在显著的点蚀现象,而在含有石墨结构的涂层中存在混合的碳化物相和片状石墨,提高了涂层的耐腐蚀性。石墨层的存在对于气缸内壁还可以起到自润滑的作用,提高了涂层的耐磨性。
刘明等研究了内孔等离子喷涂Ni45-15%Mo涂层与38CrMoAl渗氮层的耐磨性。在边界润滑条件下,涂层表面产生的MoS2和MoO2具有良好的减摩性,对提高涂层的耐磨性起到关键性作用,同时,涂层对偶件的损伤明显小于渗氮层对偶件。在实际内孔等离子喷涂过程中,缸套内壁温度高,烟尘污染严重,为了解决这些问题,王海军等人开发设计了一种具有排尘、防尘和冷却功能的内孔等离子喷涂装置,对使用前后涂层的性能进行了分析,研究发现,使用该装置可以明显降低涂层的缺陷,为制备性能优越的减摩耐磨气缸壁涂层提供了条件。
大气等离子喷涂陶瓷缸套内壁涂层具有较低的摩擦系数和优良的耐蚀、耐高温特性。毛俊元等采用等离子喷涂制备Al2O3-13%TiO2复合陶瓷纳米涂层,它具有陶瓷的高硬度、刚度和高温下极好的化学稳定性,将这种材料喷涂在金属基体表面,在一定程度上能克服陶瓷本身韧性、塑性、导热性差的缺点。李福村等也采用等离子喷涂技术,在缸套内壁制备了耐高温、耐磨损的Al2O3-13%TiO2陶瓷涂层,以增强缸套的寿命。涂层磨损机理是切削和脆性断裂或脱落磨损,其耐磨性、结合强度和抗震性等符合缸套的工作环境。Skopp等研究了混合边界润滑条件下APS喷涂低价氧化钛涂层的摩擦特性,摩擦实验选用了不同种类的活塞环对偶涂层,结果表明,TiOx涂层的耐磨性能优于灰铸铁缸套。同时,实验还发现,在酯类润滑条件下,涂层的摩擦系数减少了10%~20%,在甘醇类润滑条件下,涂层的摩擦系数从0.12降到0.04~0.06。衡量一种涂层摩擦性能的两个重要指标分别是硬度和摩擦系数,这种氧化钛陶瓷涂层的硬度约为650HV0.2,在耐磨领域具有明显的优势。
4 等离子转移弧线材喷涂
等离子转移弧(PTA)与非转移弧的区别是,非转移型等离子弧的钨级接负极而喷嘴接正极,转移型等离子弧的钨级接负极而工件接正极,后者使等离子弧在钨级和工件之间产生。实际工作中,首先要用喷嘴接正极产生等离子弧来引弧,然后工件接正极把弧引出去。等离子转移弧线材喷涂(PTWA)工艺可以喷涂几乎所有材质的实芯或药芯焊丝,对材料的要求是所喷涂的焊丝材料必须导电。
电弧电流强度对PTWA喷涂涂层的结构有较大影响。Darut等研究了不同电流强度对等离子转移弧喷涂高碳钢气缸套内壁涂层的结构与成分的影响,实验所用的电流分别为85A和150A。通过对比涂层的孔隙率发现,当电弧电流从85A增强到150A时,涂层从顶部到底端的孔隙率增加显著。实验还发现,涂层中间部位的氧化物含量最高,因为在喷涂中间过程中,系统的热量不易扩散且通风性较差,因而导致涂层氧化严重。Schramm等采用PTWA工艺在发动机气缸内壁喷涂铁基合金涂层,添加Al、Cr合金元素可以提高涂层的耐磨耐腐蚀性。摩擦实验选用线性往复摩擦试验机表征气缸壁和活塞环间的摩擦行为,实验对比了三种材料(氮化钢、类金刚石(DLC)涂层、氮化铬铝涂层)的活塞环,以寻求最佳涂层组合。与灰铸铁缸套相比,高铬、铝含量的铁基材料PTWA涂层与CrAlN涂层活塞环间的平均摩擦系数可从0.11降到0.066,表现出很大的减摩潜力,该涂层与活塞环组合应用于发动机将更经济、环保。
Rabiei等研究发现,采用HVOF和PTWA喷涂铁基丝材时,涂层中α-Fe扁平粒子之间会存在一层厚度超过100nm的非晶氧化物薄膜,为了研究该氧化层所起的作用,实验利用楔形物在光滑涂层表面加载促使该涂层产生裂纹,加载后涂层截面如图2所示(箭头标记地方是裂纹形成的地方),可以看出加压后裂纹主要在非晶氧化层处形成。从断裂韧性测试结果来看,该氧化层和α-Fe颗粒之间的结合很差,导致局部断裂韧性只有0.2~1MPa•m1/2。因此,有效地抑制该非晶氧化物薄膜层的形成,将有助于提高涂层的耐用性。
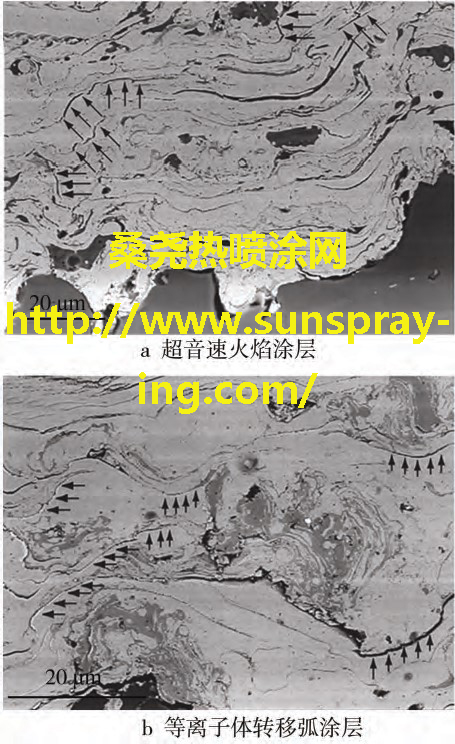
图2 加压后涂层截面局部图
Fig.2 Images of regions within cross sections taken after wedge impression: a) high velocity oxfuel (HVOF) coating,
b) plasma transfer wire arc (PTWA) coating
Edrisy等研究了PTWA工艺在铝合金表面喷涂低碳钢涂层的干摩擦特性,发现在低速高负载摩擦条件下,由于涂层中不锈钢扁平粒子断裂分层严重,涂层的磨损率最高;当速度提高、加载减小时,涂层表面生成氧化物含量较高的摩擦层,该摩擦层能够保护下面涂层免于被磨损。该课题组又研究了湿度对PTWA喷涂低碳钢涂层的摩擦磨损性能的影响,研究结果表明,在低速低负载条件下,涂层表面主要发生氧化磨损。当环境湿度增加时,磨抛变得更加活跃,涂层的磨损率降低。若在此基础上增加负载,扁平粒子的塑性变形严重,继而发生断裂和破碎。
本文由桑尧热喷涂网收集整理。本站文章未经允许不得转载;如欲转载请注明出处,北京桑尧科技开发有限公司网址:http://www.sunspraying.com/
|