金属钨涂层制备工艺的研究进展
刘艳红,张迎春,葛昌纯
粉末冶金材料科学与工程
金属钨具有非常高的熔点、沸点,极高的强度、硬度,以及很小的电子逸出功及很好的化学稳定性。但是钨储量稀少,价格昂贵,而且加工困难,直接用于制造较大型部件成本较高。因此,近百年来人们尝试采用各种方法在基体材料表面制备纯金属钨镀层,这样既能充分利用钨的优异的机械、化学及电性能,又能极大地降低制造成本。基体材料表面镀覆金属钨涂层后可广泛用作耐磨、耐蚀和热屏蔽材料,如固体火箭发动机喷管喉衬材料[1]、药型罩材料[2]、各种武器表面涂层[3]、X 射线机中的靶材[4]、微电子器件中的探针和触头以及汽车发动机的传感器等[5]。尤其是近年来在国际热核聚变堆(ITER, international thermo-nuclear experimental reactor)中用于面向等离子体第一壁涂层材料已引起了世界范围内的关注和重视[6 8]。到目前为止,制备金属钨涂层研究较多也较成熟的技术包括等离子喷涂、气相沉积、熔盐电镀等。本文重点讨论这几种制备方法的技术特点和研究现状,并对金属钨涂层的制备技术进行展望。
摘 要:金属钨属于难熔金属,具有高的强度和硬度,同时具有良好的化学稳定性,不易受到腐蚀,但其昂贵的价格及难加工特性限制了其应用,因此,用金属钨作为涂层材料来改善基体材料的性能,引起了众多研究者的关注。该文综述纯金属钨涂层的几种重要制备方法,包括:熔盐电镀法,等离子喷涂法,爆炸喷涂法,气相沉积法等。等离子喷涂是钨涂层制备中最为成熟的 1 种方法,基体材料不受限制,涂层厚度容易控制。熔盐电镀法能够通过电化学反应从化合物中一步获得厚度均匀的金属钨涂层,并且可避免引入氧和碳等杂质。化学气相沉积法获得的钨涂层致密度高;物理气相沉积法可以在任意基材上获得钨涂层。同时介绍这些方法各自的技术特点和目前的研究现状,并对金属钨涂层的制备方法进行展望。
关键词:钨涂层;电镀;喷涂;气相沉积;制备;热喷涂;等离子喷涂
1 化学镀与电镀
1.1 化学镀
化学镀(Electroless plating)也称无电解镀,是在无外加电流的情况下借助合适的还原剂,使镀液中金属离子还原成金属,并沉积到零件表面的 1 种镀覆方法。最早发现并使用这项技术是在 1944 年,美国国家标准局的 A.Brenner 和 G.Riddell 发现并弄清了沉积非粉末状镍层的催化特性,使化学镀技术的工业应用成为可能[9]。就化学镀来说,由于要在水溶液中进行,而难熔金属的沉积电位比氢离子的沉积电位更负,氢在电极上大量析出,所以难熔金属(钨、钼、锆等)除铬以外都很难从水溶液中沉积出来,因此,很难实现化学镀覆纯金属钨。但研究表明可通过化学镀工艺将钨与铁族金属以多元合金的形式镀覆到基体上[10 13]。如钨与镍可共沉积出 Ni-W 合金,在合适的镍钨合金沉积液组成和合适的沉淀条件下还可以沉积出 Ni-W-P(B)合金镀层[14 16]。
1.2 熔盐电镀
熔盐电镀法是制备金属钨镀层较有效的方法。早在 100 多年前人们就开始尝试电镀钨,通过实践发现自水溶液和有机溶剂中只能得到钨青铜或铁族金属的钨合金,只有在熔盐体系中才可以电沉积出纯金属钨。由于熔盐电镀要在较高温度下进行,电镀的同时也是沉积金属和基体金属相互固态扩散的过程,互扩散层的形成使得沉积层与基体间的结合更加牢固。目前熔盐电镀钨涂层的研究已取得一定的成果。1956 年DAVIES 等[17]首次报道从熔融的硼酸盐 钨酸盐中电沉积出钨,随后 SENDEROFF 等[18]在熔融的氟化物中得到了致密的钨镀层。根据所采用的熔盐电解质的不同,马瑞新等[19]归纳出三大熔盐体系:卤化物体系、氧化物体系和氧 卤混合物体系。目前国外研究较多的是基于卤化物体系的熔盐电沉积。如 KOJI 等[20]在250 ℃通过恒电位电解 ZnCl2-NaCl-KCl-KF 熔盐沉积出钨薄膜,他们以 WCl4作为钨源,整个沉积过程在氩气保护的手套箱中完成。通过分析,在镍衬底上沉积出厚度不到 1 μm 的纯钨薄膜层,中间有一层镍锌合金层。HIRONORI 等[21]在 ZnCl2-NaCl-KCl 熔盐体系中加入 WO3作为钨源,同时为了使 WO3较易溶解在此体系中,加入了 KF,在 250 ℃温度下采用恒电位电解法获得厚2.5 μm的钨镀层,镀层形貌如图1所示。
尽管镀层由于沉积过程中的内应力而出现了一些微裂纹,但总体上光滑致密。从以上的研究可以看到,由于卤化物体系中都要加入 KF 这种毒性物质,而且该体系一般要求进行严格的物质净化,过程复杂且较难控制,所以其应用受到了限制。
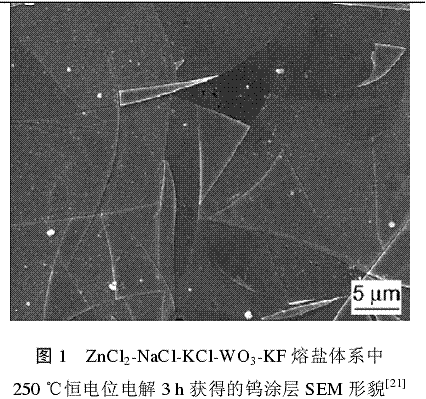
国内进行熔盐镀钨的研究始于20世纪90年代初,吴仲达[22]采用循环伏安法在LiCl-NaF-Na2WO4体系中电沉积出钨,但对于钨镀层的性能没有进行进一步的报道。文振环等[23]在 KF-B2O3-K2WO4熔盐体系中得到了平整光滑的钨镀层,并研究了工艺条件对镀层性能的影响。马瑞新等[24 25]采用 Na2WO4-ZnO-WO3体系电镀钨涂层,在空气及 850~950 ℃条件下得到表面平整的钨镀层,镀层为柱状晶。李运刚等[26 27]也对Na2WO4-ZnO-WO3体系中电沉积钨涂层做了较详细的研究。当 n(Na2WO4):n(WO3):n(ZnO) =6:2:2 时可获得30~40 μm 厚的镀层。而且在不同的基体上,获得性能良好的钨镀层的温度也略有不同,在钼基体上温度为850 ℃以上,铜基体上需 870 ℃以上,而耐热钢则需要在 890 ℃以上才能获得性能良好的钨镀层。同时也证明在电镀中选择适当的电镀参数对获得高质量镀层至关重要,如采用脉冲电流和 60~80 mA/cm2的平均电流密度最为合适。从以上各种实验结果来看,从氧化物熔盐体系中可以获得与基体结合良好的钨镀层。但仍存在许多问题,如操作温度过高可能对基体产生不利影响,而且镀层厚度相对较薄。
2 热喷涂
热喷涂是利用某种热源将涂层材料加热到熔融或半熔融状态,同时借助于焰流或高速气体将其雾化,并推动这些雾化后的粒子喷射到基体表面,沉积成具有某种功能的涂层。热喷涂主要包括爆炸喷涂、超音速火焰喷涂和等离子喷涂。
2.1 爆炸喷涂
爆炸喷涂最早由美国联合碳化物公司利德分公司发明,于 1953 年投入生产。爆炸喷涂[28]利用混合气体爆炸的能量将具有各种功能的粉末材料加热并加速轰击到工件表面上,使之形成坚固涂层。与其他喷涂工艺相比,爆炸喷涂有许多优点,如涂层与基体结合强度高,涂层致密;镀件不会发生大的变形和组织变化;涂层均匀、厚度易控制等。种法力等[29]以乙炔和氧气作为爆炸气体,将平均粒度为 8 μm 的钨粉,以每秒 5 次的爆炸频率,距铜基体 120 mm 的距离进行爆炸喷涂,并对喷涂后的涂层进行热等静压处理,以增强钨铜结合强度和涂层密度。最后获得厚度为 300μm 左右的涂层,且涂层与基体铜结合力较高。但是钨与铜的热膨胀系数和弹性模量相差很大,在加载热通量过程中,界面处产生应力,影响材料的耐热冲击性能。而且爆炸喷涂的喷涂粉末只能以直线从喷枪中喷出,所以被喷涂的基材形状不能够太复杂,再加上喷涂设备噪音大(高达 180 db)和喷涂粉末污染等问题,在一定程度上限制了此方法的应用。但因为爆炸喷涂能在大面积基体材料上进行,且杂质含量少,与基体的结合强度相对较高,所以采用爆炸喷涂方法获得钨涂层仍然是制备核聚变较低热通量区域面对等离子体材料的 1 种参考方法。
2.2 超音速火焰喷涂
超音速火焰(high velocity oxygen fuel,HVOF)喷涂是 20 世纪 80 年代发展起来的 1 种高速火焰喷涂技术[2],具有火焰喷射速度高(可达 1 500~2 000 m/s)和温度低(约 3 000 ℃)的特点[6]。简中华等[2]通过超音速火焰喷涂(HVOF)制备了钨涂层,用于新型药型罩材料。涂层的表面形貌如图2 所示。分析发现,钨颗粒加热融化不充分,主要以固态颗粒形式撞击基体,不能形成连续涂层。涂层很薄且有许多孔洞,局部区域基体铜暴露出来。由于HVOF 喷涂速度较高,喷涂火焰温度一般为 3 000 ℃左右,低于钨的熔点 3 340 ℃,因此钨颗粒不易融化。此种方法得到的钨涂层性能不是很好,但由于 HVOF喷涂的动能大,速度快,粒子在空气中飞行时间短,所以被氧化的机会小。因此可以将 HVOF 与其他制备工艺相结合以提高涂层性能,这或许将是 1 种切实可行的途径。
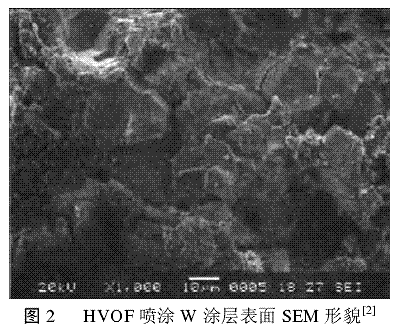
2.3 等离子喷涂
等离子喷涂技术是 20 世纪 50 年代开发出来的 1种表面处理工艺。等离子喷涂设备及工艺是采用等离子弧发生器(喷枪)将通入喷嘴内的气体(常用 Ar、N 和H 等气体)加热和电离,形成高温高速等离子射流,熔化和雾化金属或非金属物料,并使其高速喷射到经预处理的工件表面上形成涂层。等离子体喷涂是目前研究最多也最成熟的 1 种钨涂层制备工艺,最大的好处是不受喷涂基体材料的限制,既可以在金属基体如不锈钢,铜,钼等上进行,又可以在石墨,碳纤维复合材料或者碳/碳复合材料上进行。并可获得较厚的涂层,涂层性能也较好。等离子喷涂包括常压(大气)等离子喷涂,真空等离子喷涂或低压等离子喷涂。
2.3.1 常压(大气)等离子喷涂
常压(大气)等离子喷涂法采用的是常规喷涂方法,具有操作方便,生产效率高等特点。但是涂层中含有较多杂质,且致密度和结合强度不理想。Y.Yahiro等[30]在铁素体/马氏体钢上采用常压等离子喷涂钨金属层,得到的涂层厚度可达 1.0 mm,但涂层孔隙率达6%,孔洞尺寸大于 10 μm。由于喷涂过程中涂层表面被氧化,导致钨涂层热载性能较差,出现较多的裂纹。尽管采用大气(常压)等离子喷涂获得的涂层性能普遍不理想,但其技术条件相对简单,仍是 1 种非常有吸引力的钨涂层制备技术。
2.3.2 低压(真空)等离子喷涂
低压(真空)等离子喷涂(VPS)是在低压保护性气氛下进行的喷涂,其优点是焰流速度高、粒子动能大,涂层能够免受氧化和污染;基体预热温度便于提高,并且采用反向转移弧对基体表面进行电清理和活化,能够大大改善涂层与基体间的结合性能[8]。TOKUNAGA 等[31]采用真空等离子喷涂技术在炭/炭复合材料上得到了厚 1 mm 和 0.5 mm 的纯金属钨涂层。他们在真空等离子喷涂钨之前,用物理气相沉积(PVD)的方法,先在炭或 C/C 纤维复合材料表面沉积一层铼的扩散势垒层,以避免钨与炭基体形成脆性的钨的碳化物。刘翔等[32 33]也在石墨和炭纤维基体上先采用物理气相沉积法沉积出多层硅铼或者钨铼的中间过渡层,厚度约 12 μm。而在铜基体上则先喷涂梯度过渡层,约 150 μm,然后再喷涂纯金属钨,涂层总厚度达 0.3 mm,涂层形貌如图 3 所示。该涂层的密度高,导热性能好,且涂层与基体结合良好。邝子奇等[7]采用梯度涂层的方式,利用 VPS 技术成功地在铜合金基体上制备出结合强度很高的厚钨涂层(厚度> 1 mm),涂层具有良好的导热性和耐热冲击性能,能承受 9.6MW/m2和 200 s 的脉冲。可见采用 PVD 方法结合等离子喷涂产生中间过渡层和梯度过渡层是 1 种很好的制备钨涂层的手段。目前,VPS 技术已经广泛用于制备面向等离子体第一壁厚钨涂层(厚度超过 1 mm),由于该技术具有制备效率高、成本低和可以原位修复等优点,已经成为制备厚钨涂层的首选技术[6 8]。
2.3.3 惰性气体等离子喷涂
用惰性气体等离子喷涂法也可以镀覆钨金属层。LIU 等[33]采用该方法分别在 Cu 和 SMF700 石墨上获得金属钨涂层。结果显示在 Cu 基体上制备梯度过渡层后,涂层与基体的结合强度有所提高,但是热机械性能比真空等离子喷涂差很多, 200 次热循环测试就出现裂纹。而真空等离子喷涂得到的钨涂层可以承受大于 1000 次的热循环测试。葛毅成等[34]在 C/C-Cu 复合材料表面等离子喷涂金属钨涂层时通入氩气和氢气作为保护气体,以防止 W 在涂层制备过程中被氧化。分析结果表明,虽然在惰性气氛下可以避免钨粉氧化,但是涂层的性能比真空等离子喷涂差很多。
2.3.4 其他等离子喷涂法
日本的AKIRA等[4]采用1种瓦斯隧道型等离子喷涂技术,将喷涂距离从一般的 200~300 mm 缩短到40 mm 以下,用氩气作为保护气体,得到厚度分别为70 μm 和 180 μm 的钨涂层,涂层与不锈钢衬底结合较好,70 μm 厚的涂层致密,孔隙率低,180 μm 厚的涂层孔隙率较高,原因可能是喷涂过程中钨反复再熔引
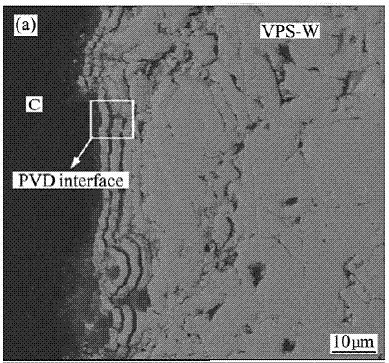 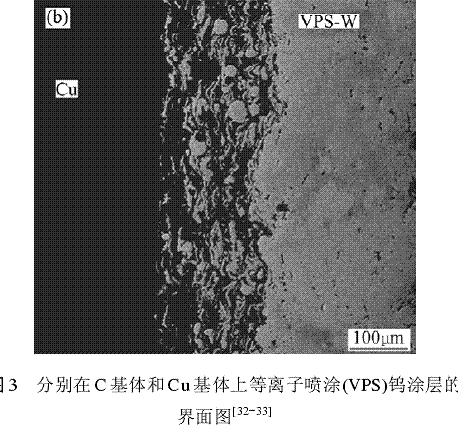
入了气孔。HYOUNGIL 等[3]采用蒸汽等离子喷涂结合热等静压的方法得到钨涂层,但是涂层的密度较真空等离子喷涂得到的钨涂层低。尽管如此,这些方法还是给出了钨涂层制备的可选择性。
以上分析结果显示,等离子喷涂是 1 种有效的、研究较成熟的镀覆金属钨的方法,得到的涂层性能依据喷涂的具体参数而定,涂层厚度可以从纳米级到几毫米。
3 气相沉积
气相沉积技术是利用气相中发生的物理、化学过程,在工件表面形成功能性或装饰性的金属、非金属或化合物涂层。气相沉积技术按照成膜机理,可分为化学气相沉积、物理气相沉积和等离子体气相沉积。目前制备钨涂层可采用物理或化学气相沉积方法,或者将气相沉积方法结合其他制备技术,提高钨涂层的性能。
3.1 化学气相沉积
化学气相沉积(Chemical vapor deposition,CVD)是 20 世纪 60 年代发展起来的,它是 1 种化学气相生长法,这种方法把含有薄膜元素的 1 种或几种化合物、单质气体供给基体,借气相作用或在基体表面上的化学反应生成所要求的薄膜。反应气体来源已由金属卤化物向羰基化合物以及其它金属有机化合物方向发展。CVD 沉积钨涂层可用氟化物及氯化物氢还原等方法获得。杜继红等[35]采用 WF6+H2体系,通过氢还原沉积钨涂层。张昭林等[36]采用氢还原 WF6沉积钨涂层。研究结果表明随着温度与沉积时间增加,涂层厚度增加。但是当温度升高到一定值时,钨会同时沉积在反应室的壁上导致实验无法进行。如沉积时间过长,沉积层增厚,表面变得粗糙,与基体的结合力变差。对于氟化物还原沉积钨涂层,氟可能会在颗粒边界聚集,增加涂层的脆性[37]。LAI 等[38]采用 W(CO)6作为前驱物,通过低压化学气相沉积(LPCVD)得到金属钨涂层。杜继红等[39]采用氯化物作为前驱物,用热分解和氢还原 2 种方法在钼基体上获得钨涂层,如图 4 所示,钨与钼之间存在 2 μm 的扩散层,涂层的抗热震性能和结合力都很好。以上研究结果说明,采用化学气相沉积法得到的钨涂层密度可达到理论密度的99%以上,这是其他方法很难达到的。同时涂层厚度可以通过调整沉积时间和沉积温度来进行控制,便于得到所需厚度的涂层。
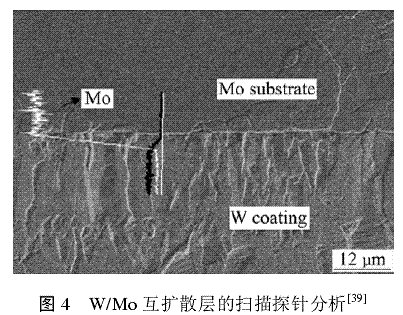
3.2 物理气相沉积
物理气相沉积技术出现于 20 世纪 70 年代末,是1 种利用物理过程沉积薄膜的技术。和化学气相沉积相比,物理气相沉积适用范围广泛,几乎所有材料的薄膜都可以用物理气相沉积来制备,但薄膜厚度不均匀是物理气相沉积中存在的问题。主要的物理气相沉积方法有:热蒸发、溅射、脉冲激光沉积等。而沉积金属钨大部分都采用溅射的方法。GANNE 等[40]通过磁控溅射在钢衬底上沉积出 0.6~30.2 μm 的钨涂层。
WANG 等[41]采用射频磁控溅射法在单晶硅衬底上得到 70~460 nm 厚度不等的钨涂层。RADIC 等[42]采用直流和射频磁控溅射技术在硅衬底上沉积出 150~200 nm 厚的钨膜,该钨膜为非晶态且热稳定性较好。MAIER 等[43]分别采用磁控溅射、电弧沉积和电子束蒸发 3 种物理气相沉积法制备钨涂层。采用磁控溅射和电弧沉积法得到 10 μm 厚的钨涂层,采用电子束蒸发的方法只得到 0.2~0.5 μm 的钨涂层,而且涂层中的轻杂质含量都高于另外 2 种方法得到的涂层,但是涂层与基体的粘附性很好,在热载测试中没有出现分层现象。电弧沉积的钨涂层粘附性也非常好,只有磁控溅射法得到的涂层与基体粘附性不理想,在热载测试中出现明显的分层现象。3 种方法得到的涂层表面形貌和均匀性都较好。此外,用 PVD 法结合真空等离子体喷涂法的文献报道较多,制备的涂层性能较好[31 33],本文前面已经进行了较详细的介绍。近年来还出现了许多新的钨涂层制备方法,如激光烧蚀技术[44],压缩等离子体流技术[45],双层辉光离子渗技术[46],但这些方法用于制备钨涂层都不是很成熟,还需要进一步深入研究。
4 展望
以上各种钨涂层的制备方法,可以归纳为电镀、热喷涂和气相沉积 3 大类。各种制备方法基本上都是基于这些方法进行的改良和探索。目前研究最为成熟的技术是等离子体喷涂和化学气相沉积。等离子喷涂不受基体材料的限制,可以应用于金属、非金属或复合材料表面钨涂层的制备,并可获得厚度不同的钨涂层,而且通过各种辅助方法使涂层与基体的结合力大大增加,能够满足实际使用的需要。化学气相沉积法得到的钨涂层的致密度是目前所有方法中最高的,但会引入杂质元素,而且其含氟或氯的前躯体会产生有害气体,应尽量避免。物理气相沉积法的优点是不受基体材料的限制,但是所制备的钨涂层较薄,最厚也只能够到几十微米。此外,熔盐电镀法是较有希望的1 种方法,可通过电化学反应获得厚度均匀的钨涂层。而且是从化合物中沉积出纯金属钨,避免了引入氧或碳等杂质元素,但基体材料受到一定限制。
随着科学技术的进步,钨涂层的使用条件愈加苛刻,而且应用范围也愈加广泛。未来钨涂层制备技术的研究集中在以下几个重要方向:1) 高质量厚钨涂层(>1 mm)的制备。近年来,随着国际热核聚变实验堆(ITER)计划的实施,聚变堆面向等离子体材料 (PFM)受到极大关注。目前已经确定全钨涂层与热沉材料组成的复合结构为 PFM 的重要候选材料,由于它是保护真空室内壁和各种内部部件免受高温等离子体直接辐照的第一道屏障,是磁约束聚变堆中运行条件最苛刻、也最关键的材料,因此,要求钨涂层具有较大的厚度。获得与热沉材料结合良好的厚钨涂层是未来聚变堆实现应用的关键之一。2) 具有功能梯度结构钨涂层的制备。由于钨涂层在热物理性能上往往与基体材料存在较大差异,如材料的热膨胀系数等,直接在基体材料上沉积钨涂层会引起较大的应力,从而降低涂层的结合强度和质量,而通过功能梯度结构设计在钨涂层与基体之间预先沉积不同成分和厚度,并按梯度分布的中间过渡层,可极大地缓解这种应力,进而提高涂层的质量。为了实施这种梯度结构的涂层制备,将几种制备技术如热喷涂和气相沉积等有效结合将是获得高质量钨涂层的关键。3) 纳米结构钨涂层也是未来研究的重要方向。纳米结构涂层由于晶粒细化和纳米尺寸效应,涂层致密度、硬度和结合强度明显提高[47],而对于钨材料更是如此,晶粒细化会明显提高材料的韧性和抗热冲击能力。
REFERENCES
[1] 刘建军, 李铁虎, 郝志彪, 等. 碳/碳复合材料表面等离子喷涂钨涂层结构与性能研究[J]. 表面技术, 2003, 32(3): 28 30.
LIU Jian-jun, LI Tie-hu, HAO Zhi-biao, et al. Study on structure and performance of plasma-spraying tungsten coatings on carbon-carbon composites [J]. Surface Technology, 2003, 32(3):28 30.
[2] 简中华, 马 壮, 王富耻, 等. 热喷涂铜基 W 涂层工艺性能研究[J]. 兵器材料科学与工程, 2007, 30(2): 27 30.
JAN Zhong-hua, MA Zhuang, WANG Fu-chi, et al. Study on high velocity oxy-fuel and plasma spraying process of W coatings on copper substrate [J]. Ordnace Material Science and Engineering, 2007, 30(2): 27 30.
[3] HYOUNGIL K, JAAFAR E A, VIJAY G, et al. Interface strength measurement of tungsten coatings on F82H substrates [J].
Journal of Nuclear Materials, 2009, Fusion Reactor Materials,Proceedings of the Thirteenth International Conference on Fusion Reactor Materials, 2009, 386/388: 863 865.
[4] AKIRA K, SHAHRAM S, NASR M G. Formation of tungsten coatings by gas tunnel type plasma spraying [J]. Surface and Coatings Technology, 2006, 200(16/17): 4630 4635.
[5] HIRONORI N, TOSHIYUKI N, RIKA H. Electro deposition of refractory metals in medium-temperature molten salts [C]//206th Meeting of the electrochemical society, 2004.
[6] 纪岗昌, 李长久, 王豫跃, 等. 超音速火焰喷涂 Cr3C2-NiCr涂层磨料磨损行为[J]. 材料热处理学报, 2002, 23(4): 34 38.
JI Gang-chang, LI Chang-jiu, WANG Yu-yue, et al. Abrasive wear behavior of HVOF deposited Cr3C2-NiCr coating [J].Transaction of Materials and Heat Treatment, 2002, 23(4):34 38.
[7] 邝子奇, 刘 敏, 邓畅光, 等. 低压等离子喷涂钨涂层性能的研究[J]. 材料研究与应用, 2008, 2(3): 191 194.
KUANG Zi-qi, LIU Min, DENG Chang-quang. et al. Study of tungsten coating sprayed by LPPS [J]. Materials Research and Application, 2008, 2(3): 191 194.
[8] 邝子奇, 代明江, 熊国刚, 等. 钼基体上真空等离子喷涂钨涂层的研究[J]. 真空科学与技术学报, 2005, 25(5): 381 384.
KUANG Zi-qi, DAI Ming-jiang, XIONG Guo-gang, et al.Tungsten coating on Mo substrate by vacuum plasma spray [J],Journal of Vacuum Science and Technology, 2005, 25(5):381 384.
[9] HENRY J R. Electroless(autocatalytic) plating [J]. Metal Finishing, 2007, 105(10): 350 360
[10] 杜 楠, 赵 晴. 化学镀镍钨磷合金过程中的析氢行为和沉积机理[J]. 南昌航空工业学院学报: 自然科学版, 2002, 16(4):18 22.
DU Nan, ZHAO Qing. Behavior of hydrogen evolution and rate determining by electrochemical method during electroless Ni-W-P alloys plating [J]. Journal of Nanchang Institute of Aeronautical Technology: Natural Science, 2002, 16(4): 18 22.
[11] 徐智谋, 郑家燊, 刘宏芳, 等. 化学镀制备功能梯度材料的实验研究[J]. 复合材料学报, 2000, 17(4): 66 70.
XU Zhi-mou, ZHENG Jia-yan, LIU Hong-fang et al. Investigation of production of functionally gradient material by electroless plating [J]. Acta Materiae Compositae Sinica, 2000, 17(4): 66 70.
[12] 李 君, 胡信国, 常立民. 钨酸钠在化学镀 Ni-W-P 三元合金镀液中行为的研究[J]. 化学世界, 1996, 37(9): 459 461.
LI Jun, HU Xin-guo, CHANG Li-min. Investigation of sodium tungstate behaviour in electroless Ni-W-P ternary alloy plating bath [J]. Chemical World, 1996, 37(9): 459 461.
[13] 赵 晴, 杜 楠, 熊友泉, 等. 化学镀 Ni-W-P 合金工艺的研究[J]. 材料保护, 2001, 34(5): 28 30.
本站文章未经允许不得转载;如欲转载请注明出处,北京桑尧科技开发有限公司网址:http://www.sunspraying.com/
|