浅谈热喷涂技术及其在海洋环境中的应用
吕建伟 刘忠斌 杨媚媚 樊志勇
涂 装
摘 要:本文简单介绍了热喷涂技术特点、原理、工艺以及热喷涂技术在防腐性能方面的优越性。
关键词:热喷涂 特点 优越性
0 引言
随着经济快速发展,人类在海洋中建造了无数固定与活动的海上钢铁构筑物,如舰船、潮汐民电设备、海底管线、栈桥码头、海上石油平台等,从20世纪中叶开始世界各国在不同的海域,对热喷涂锌铝及其合金涂层海洋环境下长期防护性能,进行了许多现场挂片暴露试验[1]。前苏联科学家1989年公布的研究结果认为,120μm厚的热喷铝层在盐水中防腐寿命可达20~25年,150μm厚的铝锌涂层(5μm 厚的锌和145μm厚的铝)在潮湿大气中防腐寿命可达40年以上。
1995年k.p.Fsicher等人的研究结果表明,热喷铝层已成为海岸及海洋环境中钢结构的重要防护方法。采用热喷涂得到的200μm厚的热喷铝层在海洋飞溅带的防腐寿命可超过30年。
1热喷涂技术的特点和种类
按涂层加热和结合方式,热喷涂有喷涂和喷熔两种。热喷涂技术按照加热喷涂材料的热源种类分为:火焰喷涂、电弧喷涂、等离子弧喷涂(超声速喷涂)、爆炸喷涂、激光喷涂和重熔、电子束喷涂。按喷涂材料的种类和形状,热喷涂又可分为粉末喷涂和线材喷涂。热喷涂技术的特点包括以下几点:(1)基体材料不受限制,可以是金属和非金属,可以在各种基体材料上喷涂;(2)可喷涂的涂层材料极为广泛,热喷涂技术可用来喷涂几乎所有的固体工程材料,如硬质合金、陶瓷、金属、石墨等;(3)喷涂过程中受热程度可以控制,基体材料温升小,不产生应力和变形;(4)操作工艺灵活方便,不受工件形状限制,施工方便;喷涂既可在整体表面上进行,也可在指定区域内涂敷,既可在真空或控制气氛中喷涂活性材料,也可在野外现场作业。(5)生产率高,大多数工艺方法的生产率可达到每小时数千克,有些工艺方法可高达50kg/h以上。
2热喷涂原理
热喷涂技术是表面工程技术中的一个重要分支,它是通过火焰、电弧或等离子体等热源,将某种线状和粉末状的材料加热至熔融或半熔融状态,并将加速形成的熔滴高速喷向基体形成涂层。涂层具有耐磨损、耐腐蚀、耐高温和隔热等优良性能,并能对磨损、腐蚀或加工误差引起的零件尺寸减小进行修复。
3热喷涂工艺
热喷涂工艺主要包括:工件表面制备、喷涂、涂层后处理。其中喷砂是非常重要的一道工序。被广泛接受的标准是,要想取得长期的保护性能,喷砂等必须达到出白级(SSPC-SP 5)。对于表面粗糙度的规定通常为75~112μm。零件喷完砂后,应尽可能在短时间内进行喷涂。
喷涂后的涂层大多存在孔隙,会降低涂层的抗腐蚀性能和绝缘性能,喷涂后必须对涂层进行封闭,通常是用石蜡作封闭剂,也有用酚醛树脂或环氧树脂进行封孔处理的。封闭后的涂层根据需要可涂中间漆和面漆,常用的有丙烯酸聚氨酯面漆和氯化橡胶面漆等。
4电弧喷涂的原理及设备
电弧喷涂是目前工业生产中应用最广泛的热喷涂方法。电弧喷涂的原理是将两根金属丝端部送到某一点,在两丝端部间加以维持直流电弧(或交流电弧),使丝材熔化,再用压缩空气穿过电弧和熔化的液滴使之雾化,以一定的速度喷向基体(零件)表面而形成连续的涂层。电弧喷涂的原理图如图1所示。电弧喷涂的主要设备包括直流电源、喷枪、送丝装置及压缩空气系统等,主要设备是喷枪。影响喷涂层密度的主要因素为压缩空气的压力和流量,以及喷涂枪的喷嘴几何形状。影响喷涂熔滴氧化的主要因素为喷枪电弧电流。影响喷涂层结合强度的主要因素有喷嘴结构、压缩空气的压力和流量、被喷涂工件表面预处理程度、喷枪喷嘴相对工件的距离、电弧电压以及送丝速度。
5电弧喷涂与其他热喷涂方法的特点比较
在电弧喷涂的过程中,电弧最高温度可达5000℃,设备相对简单,便于现场施工。与超音速火焰喷涂技术、等离子喷涂技术、爆炸喷涂技术相比,电弧喷涂设备体积小,重量轻,使用、调试非常方便,而且结合强度较高,成本低。表1为几种热喷涂工艺的性能比较。6钢铁构件几种防护方案的特点目前,我国钢铁构件的涂层防护方案主要有:油漆防护(目前为止仍是最广泛使用的方案),热浸镀锌防护和热喷涂锌、铝防护。三种实用户外钢铁构件防护工艺特点如表2所示。从表2可以看出,热喷涂防腐
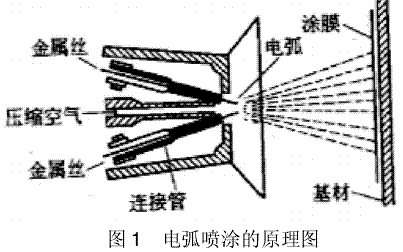 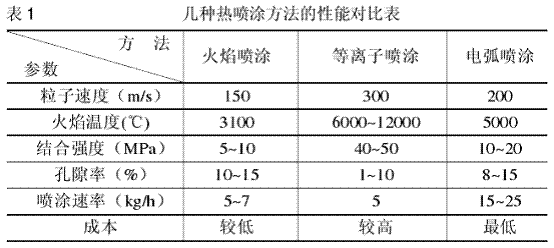 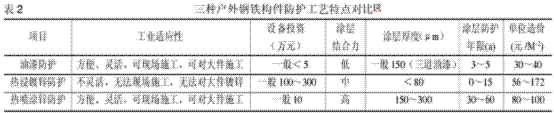
因。施工人员应保证适当调节喷枪,在距表面的最佳距离施工涂料,确定涂料在表面上充分流动,润湿表面并以多道薄层和重叠5 0%的方式施工涂料也能有效地防止起泡。(3)为使涂料充分固化,所有溶剂必须全部挥发,所以,挥发型涂料不应施工太厚的涂膜。如果施工过厚涂膜,可能会有溶剂残留在涂层内部。残留溶剂处在溶剂挥发后最终变为空隙,形成气泡。
3涂层起泡的控制
综上所述,根据涂层起泡的原因分析涂层起泡控制可从下面三个方面下手:一是涂料生产过程控制,比如溶剂挥发率或树脂含水率、颜填料吸湿性等;二是涂层设计,比如不同类型涂层的搭配、阴极保护区域内涂料的选择等;三是涂料施工时的控制。首先,要加强生产管理。涂料生产时,严格控制所用颜料、填料及溶剂的含水量;在底漆配方中,尽量避免使用可溶性的填料;使用溶剂要兼顾其挥发平衡,避免溶剂过多残留;在高湿环境中,使用渗透性低的基料。其次,应尽量按照专业涂层设计人员的设计进行施工,或尽量采用具有认证机构认证的涂装配套系统,避免因不搭配的涂层施工造成涂装缺陷。最后要加强施工管理。施工时要避免高温、潮湿等不良气候环境,被涂装表面温度应保持在露点温度3摄氏度以上,相对湿度不高于85%;施工前如果涂层遇雨或凝露、结霜等,要使其干燥后,方可涂刷下一道涂料;施工时应根据涂料说明书在涂料公司的技术服务的指导下进行施工,采用合理的施工修补方法相搭配,特别注意双组分涂料应有一定的熟化期,从而避免混合不均匀和反应产生热,引起气泡;控制涂层厚度,降低其透水性;控制表面处理的最终状态,注意表面粗糙度、表面清洁度。粗糙度太大易产生漏涂、空穴,必然引起气泡;待涂表面一定要保持清洁,不得留下电解质、粉尘、油脂等影响涂料附着力的杂质;制品使用和保存时,尽量避免高温、高湿环境,减少直接与水接触的机会;涂刷多孔性基材时,应先涂刷渗透性好的封闭底漆或喷涂防泡层,尽量驱除孔内残留空气、溶剂等残留物。
4结语
综上所述,涂层的起泡原因比较复杂,我们应针对不同成因造成的起泡缺陷进行分析,根据其产生的原因采取控制措施,避免在生产和使用中的涂层起泡现象,从而得到一个完美的涂层,取得装饰和防护俱佳的效果。
参考文献
[1] NACE初级培训教材.
[2]庞启财.防腐蚀涂料涂装和质量控制.北京.化学工业出版社.
本站文章未经允许不得转载;如欲转载请注明出处,北京桑尧科技开发有限公司网址:http://www.sunspraying.com/
|