热喷涂纳米粉体材料及其涂层制备
梁秀兵,邓智昌,许 一,徐滨士
材料工程2002
摘要:介绍了国外喷涂用纳米结构喂料的制备方法,以及采用几种先进的热喷涂技术制备的纳米结构涂层,并指出非晶/纳米晶涂层是该领域研究的重中之重。与传统喷涂层相比,纳米结构涂层在耐磨、防腐性能方面呈现出优异性能和良好的发展前景。
关键词:纳米粉体;热喷涂;喷涂喂料;非晶/纳米晶涂层
热喷涂技术是表面工程领域中十分重要的技术,其发展趋势是:设备方面(喷涂枪)向高能、高焓、高速度发展;材料方面向系列化、标准化、商品化方向发展,以保证多功能高质量涂层的需要;工艺方面向机械化、自动化方向发展,如计算机控制、机械手操作等。随着纳米粉体材料的研究与发展和各种新型、优质热喷涂技术(如高速火焰喷涂(HVOF)、高速电弧喷涂(HVAS)、超音速等离子喷涂(SPS)等)不断涌现,纳米结构涂层的热喷涂正在成为热喷涂技术重要的发展方向。与传统涂层相比,纳米结构涂层在强度、韧性、抗蚀、耐磨、热障、抗热疲劳等方面会有显著改善,且部分涂层可以同时具有上述多种性能。热喷涂技术中纳米粉体材料研究的基础问题有纳米粉体材料热喷涂层与基体间的界面问题;纳米粉体材料在热喷涂层动态制备过程中的物理、冶金、化学等过程;热喷涂层中纳米粉体材料与其它材料之间的协同效应。
1 纳米粉体材料热喷涂喂料的制备
通常喷涂粉的粒度范围为-140~+325目,有些陶瓷粉可细到5μm左右。过细的粉末会产生烧损和飞扬等问题,送粉加大困难,沉积效率也受影响。近些年,由于高速火焰喷涂(HVOF)和高功率等离子喷涂(HPPS)的出现,使喷涂向细微级靠近。HVOF和HPPS焰流和颗粒飞行速度高,缩短了颗粒在焰流中的受热时间,大粒度颗粒在未熔化之前就已达到基体表面,难以形成理想涂层,而粉末细化,可改善这一状况。当前,有些公司已推出专门用于HVOF喷涂的系列粉,粒度范围常在-270~+500目之间。
纳米粉体不能直接用于热喷涂,主要原因也是有两个:一是粒径(1~100nm)和质量太小,二是喷涂过程中容易烧结。解决问题的办法是将纳米粉体材料制备成能够直接热喷涂的纳米结构喂料(Nanostruc-ture Feedstock)。目前,制备热喷涂纳米结构喂料主要采用液体分散喷雾法和机械研磨合成法[1]。
液相分散喷雾法工艺稳定性好,能够批量生产,该法可用图1所示流程表示。粘合剂应能溶解在分散介质(水或有机溶剂)中,具有一定粘结性能,且为无灰型的高聚物,如醋酸纤
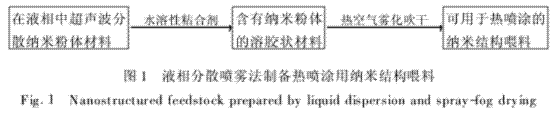
维素,硝基纤维素等。制备的纳米结构喂料要求是圆球形的,结构致密,并且粒度分布均匀,以保证喂料在送粉系统中具有良好的流动性。
机械研磨合成法是通过机械研磨、机械合金化、高能球磨等方法直接将微米粉或非晶金属箔加工成纳米结构喂料。具体的加工过程为:在干燥的高真空料机内通入Ar气(或N2)作保护气,或在CH3OH和液N2介质中,通过对磨球/粉体质量比、磨球数量和尺寸、能量强度、球磨温度、介质等参数的控制,在高速运转的硬质高能磨球与研体之间相互碰撞作用下,对粉末粒子反复进行熔结、断裂、再熔结,使晶粒不断细化,达到纳米尺寸。在除去CH3OH和液N2介质后,纳米颗粒会因自身的静电引力自行团聚为微米级的纳米结构喂料。
2 热喷涂纳米结构涂层
热喷涂技术是制备纳米结构涂层最好的技术之一,同时也是最有发展前景的技术。据文献报道[2,3],这些技术包括高速火焰喷涂(HVOF)、真空等离子喷涂(VPS)、高能等离子喷涂技术(HEPS)、双丝电弧喷涂(TWAS)等其它新的热喷涂技术。
通常情况下,燃料种类(C3H6, C2H2, H2等)、燃气比、喷涂距离(以上对HVOF技术而言)、功率大小、电流电压值高低、等离子弧流速度(Subsonic orSupersonic)、离子气和送粉气比例(以上是对PS技术而言)、喂料速度、基材温度等参数对纳米粒子的氧化程度、粒子长大、涂层致密度、结合强度等有影响。
2.1 高速火焰喷涂纳米结构涂层
高速火焰喷涂(HVOF)因其相对较低的工作温度,纳米结构喂料承受相对较短的受热时间,以及形成的纳米结构涂层组织致密、结合强度高、硬度高、孔隙率低、涂层表面粗糙度低等而倍受推崇。M.L.Lau等人[4]将45μm±11μm的Cu粉与10% (质量分数,下同)的Al粉混合经过机械冶金后获得具有非晶/纳米晶结构的喷涂喂料,然后通过HVOF技术喷涂到不锈钢基体上。涂层的TEM分析表明,涂层是由纳米晶的Cu和非晶的Al2O3组成,非晶/纳米晶涂层的成功制备对提高涂层的防腐蚀性能具有重要意义。A.H.Dent等人[5]的研究表明,HVOF技术喷涂WC/Co系列纳米结构喂料形成的涂层,尤其是WC/12Co和WC/15Co纳米结构涂层与WC涂层相比具有更加优异的耐磨性能, Co元素的添加对提高涂层耐磨性有益。采用HVOF制备了纳米结构的WC-Co涂层,从涂层组织中观察到纳米级WC微粒散布于非晶态富Co相中, WC颗粒与基相间结合良好。涂层显微硬度明显增加,涂层耐磨性提高。目前, HVOF技术被认为是制备高温耐磨涂层较为理想的技术, WC/Co系列纳米结构涂层的成功制备将大大拓宽HVOF技术在耐磨领域的研究前景。
2.2 等离子喷涂纳米结构涂层
美国Inframat纳米材料公司[6]采用真空等离子喷涂(VPS)技术喷涂Al2O3-TiO2纳米结构涂层,其制备过程如图2所示。

用上述方法获得的纳米结构涂层,在涂层致密度为95%~98%时,涂层结合强度、抗磨粒磨损能力比传统微米级粉未涂层均提高4倍左右,显微硬度达到HV900~1050,抗热冲击性能也显著改善。T.D.Xiao等人[7]采用Metco9MB等离子喷涂纳米结构Al2O3/TiO2(13% TiO2)喂料,并将获得的纳米结构涂层与传统粉末喷涂层相比。研究表明,在n-Al2O3/TiO2涂层中,单个的Al2O3纳米晶粒与TiO2纳米晶粒之间有较好的润湿性。TEM分析表明,传统粉末涂层与纳米结构涂层中扁平状粒子平均尺寸均为40μm左右,传统粉末喷涂层中的扁平粒子是由微米级粉末变形生成,而纳米结构涂层是由纳米结构喂料中的纳米尺寸晶粒组成。实验表明,纳米结构涂层的耐磨性与传统粉末喷涂层相比提高了3~8倍。D. G. Atteridge等[8]采用高能等离子喷涂技术(HEPS)喷涂WC/Co微米级纳米结构喷涂喂料,获得纳米结构等离子喷涂层。分别对传统微米级实心粉(WC/12Co)、微米级纳米结构空心喂料(WC/12Co)和实心喂料(WC/12Co)三种高能等离子喷涂层的磨损性能进行了对比分析,结果显示,实心喂料涂层的冲蚀磨损率是空心喂料涂层的1/2,是传统实心粉涂层的1/3左右。由于高能等离子喷涂采用200kW以上喷涂系统,使得纳米结构喂料在喷涂过程中熔化效果较好,粒子冲击基体的速度高,获得的涂层具有组织致密,孔隙率低,结合强度高等特点。从目前国外研究状况来看,等离子喷涂纳米结构涂层的开发研究的相关报道比较多,也是最有可能实现广泛实用化的纳米粉体材料热喷涂技术。
2.3 电弧喷涂纳米结构涂层
电弧喷涂制备纳米结构涂层的设计思想如图3所示。首先将纳米粉体材料制备成微米级的纳米结构喂料,然后以喂料和其它合金元素为芯,以金属为外皮制备电弧喷涂用粉芯丝材,喷涂后获得纳米结构电弧喷涂层。
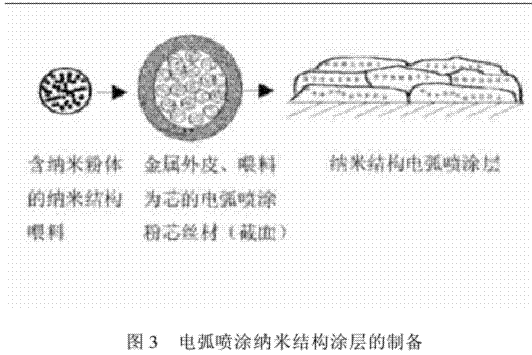
美国D. G. Atteridge和M. Becker等人[8]进行了双丝电弧喷涂(TWAS)纳米结构涂层的研究工作,喷涂粉芯丝材组成如表1所示,其中外皮和芯材料的体积比为1∶1,喷涂粉芯丝材的电压要比喷涂实心丝材时低。
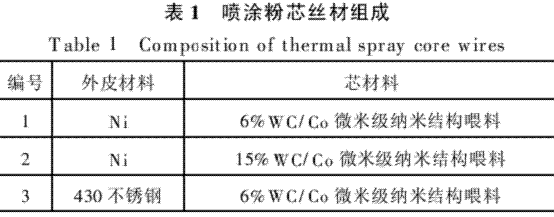
采用TWAS技术将以上三种丝材喷涂到经过喷砂预处理的碳钢基体上,喷涂电流200A,喷涂电压25~35V,喷涂厚度为1mm。对喷涂后的涂层成分分析表明,三种电弧喷涂层中, Co为15%时,喷涂层中纳米晶WC含量为25%左右;Co含量为6%时,喷涂层中的纳米晶WC含量为30%左右。随着WC含量的增加和电压的升高,涂层的耐磨性得到改善。冲蚀磨损实验表明,430不锈钢-WC/6%Co粉芯丝材纳米结构喷涂层的耐磨性能优于Ni基喷涂层。Ni基纳米结构涂层的结合强度大于60MPa,涂层的结合强度也随着涂层中纳米晶WC含量的增加而略有增加。三种涂层的结合强度测试分别为:编号1-52MPa,编号2-63MPa,编号3-71MPa。Ni基纳米结构涂层的孔隙率为3%, 430不锈钢基纳米结构喷涂层的孔隙率为7%。电弧喷涂纳米结构涂层技术由于其相对较低的设备成本和涂层呈现出优异的性能,将会成为纳米粉体材料热喷涂技术开发的一个重要方向。
目前,国外用热喷涂方法研究开发的纳米结构涂层主要有: WC/Co系列, Ti/Al等金属间化合物,ZrO2, Al2O3/ZrO2, Al2O3/TiO2, 316不锈钢, Cr2O3,Si3N4,生物陶瓷等[9,11]。其中,对热喷涂WC/Co系列纳米结构涂层研究最多,主要用于高温耐磨领域。
3 纳米粉体热喷涂存在的问题及其发展前景
利用热喷涂技术组装纳米结构涂层是一项复杂的技术,由于研究开发时间较短,涂层还不能达到设计要求,涂层结构粒子多为100~200nm左右的亚微粒子,未真正达到纳米级,涂层致密度也不够高[1]。由于粒子在室温下产生小尺寸效应的颗粒尺寸是小于100nm,且粒子强度总体上遵守Hall-Petch关系——粒子越小,强度越高。从这个意义上讲,涂层性能还没有突破性进展,利用热喷涂技术生成纳米结构涂层的发展空间还很大[1]。目前,国内在该领域的研究水平与美国等发达国家相比还有较大差距。国内热喷涂纳米粉体材料的研究尚处于试验研究阶段,从已有的研究结果来看,用热喷涂技术制备的纳米结构涂层防腐、耐磨性能优异,具有良好的应用前景,涂层的制备成本还限制着该技术的广泛应用。目前我国也加强了非晶纳米晶结构涂层的研究力度,相信,不久的将来,热喷涂纳米粉体材料技术将在我国经济建设中发挥重要作用。
参考文献
[1] Xu Binshi, Ou Zhongwen, Ma Shining etc. Nano-surface engi-neering [J]. China Mechanical Engineering, 2000, 11 (6): 707.
[2] G E Kim, V Provenzano, E J Lavernia. Vacuum Plasma Spray Applications of nanostructure Composite Coatings [A]. Ther-mal Spraying Processing of Nanoscale Materials [C]. Quebec City, 1999.
[3] Maher Boulos and Francois Gizhofer. Supersonic Induction Plas-ma Spraying of High Density Nanostructure Ceramics [A].Thermal Spraying Processing of Nanoscale Materials [C]. Que-bec City, 1999.
[4] M L Lau, R Schweinfest, E J Lavernai etc. Microstructure evo-lution of nanocrystalline Cu-Al particles during HVOF thermal spraying [A]. Thermal Spraying Processing of Nanoscale Mate-rials [C]. Quebec City, 1999.
[5] A HDent, S Sampath, HHerman etc. The effect of powder pro-cessing method on the physical properties of nanocomposite WC/Co thermally sprayed coatings [A]. Thermal Spraying Process-ing of Nanoscale Materials [C]. Quebec City, 1999.
[6] T D Xiao, S Jiang, Y Wang etc. Thermal spray of nanostruc-tured Alumina/Titania feedstock for improved properties [A].Thermal Spraying Processing of Nanoscale Materials [C]. Que-bec City, 1999.
[7] D G Atteridge, R Davis, M Scholl etc. High-energy plasma spray coating using micrometer-and nanometer-scale Tungsten Carbide-Cobalt powder [A]. Thermal Spraying Processing of Nanoscale Materials [C]. Quebec City, 1999.
[8] D G Atteridge, R Davis, M Becker etc. Twin wire arc and high-energy plasma spray coating using nanometer scale WC/Co in powder-filled cored wire. Thermal Spraying Processing of Nanoscale Materials. Quebec City, 1999.
[9] M Gell and E Jordan. Development and Production Implementa-tion of nanostructured Coatings[A]. Thermal Spraying Process-ing of Nanoscale Materials [C]. Quebec City, 1999.
[10] R Rigney. Commercialization of Thermal Spray nanomaterial coatings: Lessons Learned, Challenges and Future Opportuni-ties [A]. Thermal Spraying Processing of Nanoscale Materials[C]. Quebec City, 1999.
[11] S G fishmanm. The ONR Program on Science &Technology of Thermal Barrier Coatings[A]. Thermal Spraying Processing of Nanoscale Materials [C]. Quebec City, 1999.
本站文章未经允许不得转载;如欲转载请注明出处,北京桑尧科技开发有限公司网址:http://www.sunspraying.com/
|