残余应力对金属/陶瓷梯度热障涂层的结合强度、抗分层断裂能力、热疲劳寿命等性能有很大的影响,因此研究金属/陶瓷梯度热障涂层整体和各层残余应力的变化情况,对指导涂层制备、分析涂层性能改善的原因和失效模式具有重要意义。在金属/陶瓷梯度热障涂层的制备过程中,涂层的残余应力主要由淬火应力和热失配应力两部分构成,随着陶瓷组分的增长,涂层残余应力的形式由淬火应力主导转变为热失配应力主导,残余应力在试样边缘存在明显的应力集中现象。由于金属/陶瓷梯度热障涂层内部缺陷多、成分分布复杂、性能影响变量多,实验测得的数据往往存在局部性,涂层的实际残余应力不能得到准确的测试。目前各层涂层残余应力的具体分布状态,多用有限元软件进行模拟分析。涂层实际的成形方式并非一体成形,其内部仍存在多个界面,界面是涂层性能薄弱区域,因此需要对涂层表面和内部各层之间的界面进行重点分析。五层梯度涂层各层表面及界面残余应力沿涂层半径的分布如图所示,可以发现,残余应力在样品边缘具有明显的应力集中现象,由金属涂层到陶瓷涂层的界面径向应力由拉应力变为压应力,涂层表面的高径向应力会促进表面垂直裂纹的形成而导致涂层表面开裂。此外,陶瓷顶层表面的径向应力状态与其厚度有关,随着厚度的增加,表面径向应力由拉应力变为压应力,在制备过程中厚度越薄越容易发生表面开裂,同时当厚度达到一定程度时,能消除径向应力在边缘集中的现象。界面最大轴向压缩应力和拉伸应力分别出现在试样边缘的顶部/底层界面和基体/粘结层界面附近,远离试样边缘,轴向应力迅速减小。界面的剪切应力以压缩应力为主,在粘结层与过渡区域界面处达到最大值。靠近界面和试样边缘的应力集中程度较大,较大的拉伸和压缩轴向应力,可能分别导致面产生微裂纹和涂层的屈曲、分层开裂。总厚度相同但层数不同的双层、三层、五层热涂层的最大径向、轴向和剪切应力所示,表明有梯度过渡层的加入和层数的增加,减小了不同材料热膨胀系数的失配程度和涂层内部的温度梯度,能够显著地降低涂层整体的残余应力水平,但并没有变残余应力的分布规律,三种涂层的最大残余应力分布位置仍然一致,最大径向应力和最大轴向应力在陶瓷层以下,最大剪切应力均在粘结层以上。涂层层数的增加能够改善涂层的抗热疲劳性能,但并不能改变涂层的失效形式。此外,涂层冷却速率、基体厚度、涂层成分梯度和性质等因素,影响着金属/陶瓷梯度热障涂层残余应力的应力水平。涂层的冷却速率越大,涂层试样与环境的热对流系数越大,意味着更多的热量被散发到周围的环境中,传导到相邻层的热量越少,扁平粒子成形过程中的冷却速度变快,使得涂层径向应力变大,但涂层的剪切应力和轴向应力值变化不大。当成分梯度变化非常小或非常大时,富金属区和富陶瓷区的应力发生急剧变化。当成分线性分布时,涂层内部的残余应力沿厚度方向缓慢增加,相邻层间的应力不连续度显著减小;涂层表面和富陶瓷区附近的应力随陶瓷材料弹性模量的增加而逐渐增大;涂层表面残余应力的大小随基体厚度的增加而增大。而造成这些现象的本质原因,鲜有报道。因此,由于金属/陶瓷梯度热障涂层残余应力的重要性和其本身分布的复杂性,导致影响因素众多,在实际涂层设计过程中,利用有限元软件根据具体情况对涂层残余应力先进行分析,再依据分析结果进行具体的涂层设计变得十分重要。
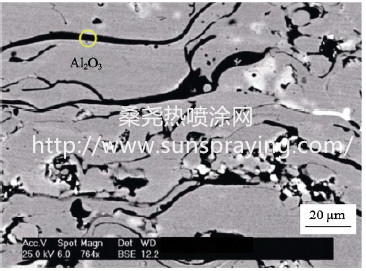
本文由桑尧热喷涂网收集整理。本站文章未经允许不得转载;如欲转载请注明出处,北京桑尧科技开发有限公司网址:http://www.sunspraying.com/
|